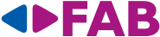
FAB Pro.Work
“This allowed our employees to spend less time on technology-related issues, and more time with customers...”
FAB Pro.Work is a commercial printer with a higher purpose. Operating as a separate business unit within FAB (over 650 people), FAB Pro.Work is a print service provider which, in addition to 11 staff members, employs 26 people who are physically challenged or have learning difficulties. FAB Pro.Work offers these people a work opportunity in a professional environment, and tries to pave the way for them to enter the open labour market. These people are mostly responsible for the order handling process and the various finishing aspects of print jobs. Under the motto “Print is our Business”, FAB Pro.Work focuses on providing digital print services, but also offers traditional offset products through a partner organisation.
The challenge
In 2009 FAB Pro.Work was facing financial difficulty due to its high running costs and declining revenues. According to Mrs Sandra Raninger, Operations Manager at FAB Pro.Work, it was necessary to restructure the organisation and to build a much more cost-efficient print production process.
The solution
During this process, FAB Pro.Work spoke to Konica Minolta and realised there were real opportunities to reduce costs and improve efficiency in the production process. Amongst other hardware and software solutions that were considered, they realised they could standardise and automate the order acceptance and job preparation process, which had involved many manual touch points. Under the new system, job tickets could be generated up-front with AccurioPro Flux, creating a far more streamlined production workflow.
This allowed the operators to pay more attention to other parts of the production process and significantly reducing the production turn-around time. The management of FAB recognised that the new solutions would deliver the necessary cost reductions and productivity improvements, and approved the plan, leading to full implementation in 2011.
The result
More than a year later, it became clear that the new solutions had indeed made it possible for FAB Pro.Work to become successful again. The total cost of the print production process was reduced by almost 50%. There was also a significant reduction in the amount of time needed to accept and prepare print jobs, which allowed employees to spend less time on technology-related issues and more time with customers, improving customer service.
Future outlook
With the new and improved workflow process in place, FAB Pro.Work is now looking to expand its business. One of the first areas of expansion the company initiated was to discuss with BBRZ holding, which FAB is part of, the possibility of having bigger print jobs at the various sister companies routed to FAB Pro.Work.
In essence, the company is seeking to act as a central reprographic department for its sister companies within FAB, further increasing print volumes. “The future is bright,” explains Sandra Raninger. “With the standardisation in our workflow processes now in place, we have room to expand. And if we had added a web-based print job submission tool for our sister companies, we would not just have optimised our internal workflow, but also made it easier to have customer submit jobs to us!”
Does the experience of FAB PRO.WORK sound like something you might like to repeat at your company?
For more information about how to streamline your workflow automation, or to speak to one of our experts, just click on Contact Us!